- Diesel Forklift
-
- 4.5 Ton Diesel Forklift48 Ton Diesel Forklift3 Ton Diesel Forklift3.5 Ton Diesel Forklift2.5 Ton Diesel Forklift33 Ton Diesel Forklift15 Ton Diesel Forklift10 Ton Diesel Forklift8 Ton Diesel Forklift4 Ton Diesel Forklift6 Ton Diesel Forklift2 Ton Diesel Forklift1 Ton Diesel Forklift1.8 Ton Diesel Forklift1.5 Ton Diesel Forklift6 Ton Diesel Forklift4 Ton Diesel ForkliftFour Wheel Drive Forklift
- Electric Forklift
-
- 12t Lithium-Battery-forklift12t Electric Forklift Truck8t Electric Forklift10t electric forklift truck25ton Lithium Battery Forklift7ton Electric Forklift16ton Lithium Battery forklift2 Ton Electric Forklift1.8 Ton Electric Forklift6 Ton Electric Forklift1.5 Ton Electric Forklift1 Ton Electric Forklift2.5 Ton Electric Forklift3.5 Ton Electric Forklift3 Ton Electric Forklift4.5 Ton Electric Forklift5 Ton Electric Forklift3 Ton Electric Forklift4.5 Ton Electric Forklift1.6 Ton Three Wheel Forklift2 Ton Three Wheel Forklift
- Forklift Attachements
-
- Fixed Short Arm non-sideshiftingnon-sideshiftingFixed Short Arm non-sideshiftingNon-sideshiftingHinged ForksCaton ClampRotatornon-SideshiftingTire ClampsPusherTurning Fork Clampsnon-sideshiftingLog HolderSideshiftingBroke Paper ClampsSideshiftingSideshiftingSingleLoad StabilizerFork PositionersSingle Double Pallet Handler
Lead acid? Lithium battery? Hydrogen fuel cells? For forklifts, this is a question worth thinking about!
Date: 2022-05-18 View:
Lead acid? Lithium battery? Hydrogen fuel cells? For forklifts, this is a question worth thinking about!
Lead-acid batteries, lithium technology or fuel cells? If you want to work cost-effectively, you must determine the most suitable energy system for your specific transportation process. This decision depends on many factors and therefore requires a high degree of experience.
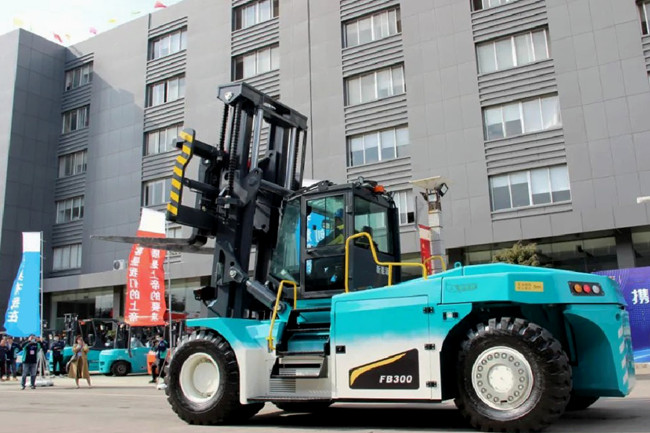
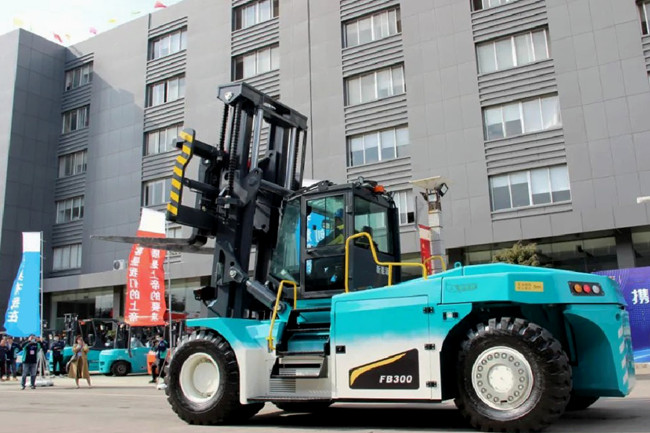
The topic of energy is becoming more and more important in intralogistics. The EU wants a climate-neutral economy by 2050 at the latest, and Germany wants it even sooner. This means that carbon dioxide emissions must be avoided as much as possible, or stored to the same extent as emissions. To achieve this, the European Commission and the federal states are currently using laws and regulations that oblige everyone to make their own contribution. For example, high carbon dioxide taxes, expensive emissions certificates, and a blanket ban on internal combustion engines will make every type of vehicle electric-driven by 2030 at the latest.
In addition, consumers are also increasingly sensitive to the climate neutrality of services and products. It is also for this reason that companies are increasingly ensuring that their supply chains are sustainable. For example, suppliers must provide certificates on the origin of raw materials, production conditions and carbon footprint. Therefore, a good ecological balance sheet is increasingly becoming a competitive advantage.
Find the right energy system
Find the right energy system
In any case, the following applies across Europe: Energy is precious and is becoming more and more precious, therefore, the consumption and use of energy must be managed intelligently. In intralogistics, this starts with selecting the appropriate energy system for the drive of the industrial truck. Current options are lead-acid batteries, lithium-ion technology or fuel cell systems. But no matter which system is chosen, the decision will have repercussions. About the infrastructure of warehouses and production facilities, about the choice of transportation system, about operating costs, and ultimately about the size of the investment. Dyrk Draenkow, Product Manager for Energy Systems, explained in a recent webinar hosted by the Hamburg, Germany-based intralogistics company STILL: "Each of these energy systems has its own characteristics that require certain prerequisites when handling" . He said that in order to arrive at a sustainable, cost-effective decision, the big picture must be considered: the transportation process, the required handling performance, the type of forklift truck and, of course, the warehouse infrastructure.
Suitability criteria
Fuel cell system
Suitability criteria
According to Björn Grünke, Product Manager Energy Systems Germany, there are therefore five criteria that can be used to determine the system that best suits the respective requirements: vehicle availability, consideration of infrastructure, acquisition and operating costs, and future safety. According to the expert, the overall result for lead-acid batteries is rather mediocre in this consideration. While they were mediocre in terms of vehicle availability, they were completely unconvincing in terms of infrastructure due to their high storage space requirements. On the other hand, when it comes to investment costs, they get ahead. Compared to all known energy systems, the purchase price of lead-acid batteries is very low, around 150 euros per kWh. However, this advantage is offset by the system's only moderately efficient operating costs. And speaking of future-proofing, this energy system can only partially convince STILL's experts. "The technology has run out!" Dyrk Draenkow said: "No further developments, namely significantly shorter charging times or higher power densities, are expected. However, if we do not take into account the stated limitations, this type of battery will have a future in It will remain a reliable, very usable energy system for a few years. It is especially useful for users who only need a few cars for a few hours of work."
Lithium battery technology
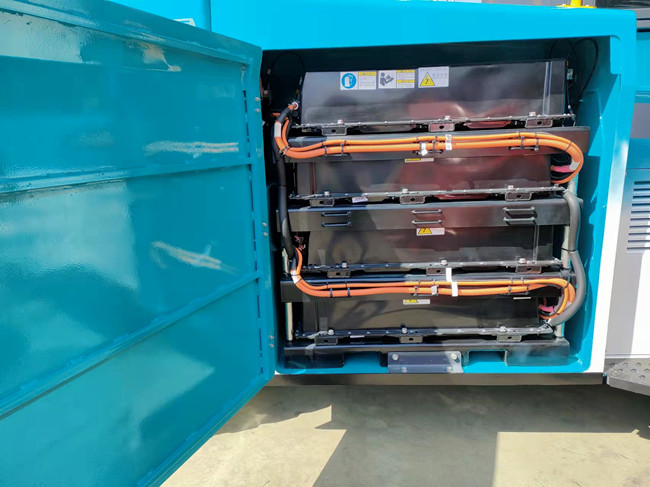
Lithium battery technology
Lithium-ion batteries can be temporarily charged at any time, and for a short period of time without damaging the battery or shortening its life. This allows the vehicle to be used flexibly, around the clock, without having to replace the battery. Lithium battery technology therefore ensures maximum availability, even in multi-shift work. Regarding charging time, experience has shown that one hour of charging means up to 3 hours of driving time. Furthermore, this energy system has very low infrastructure requirements. When it comes to investment costs, things are a little different. Because the purchase price of lithium batteries is still about two to three times higher than that of lead-acid batteries. "However, lithium-ion batteries have at least twice the lifespan at the same capacity. If you look at the overall price development of lithium-ion batteries since 2010, the direction is clear: it's getting cheaper and cheaper. The system also scored points in the future-proofing area. Charging options, as well as control options to improve efficiency, are continually being further developed, while also reducing system acquisition costs.
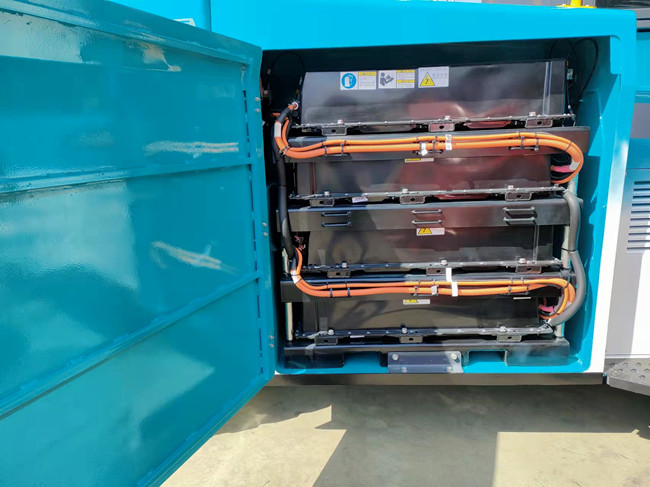
Fuel cell system
What is special about this energy system is that the electricity is generated inside the car and no longer comes from an outlet. Dyrk Draenkow said: "When we talk about fuel cells in intralogistics, we mean so-called battery replacement modules. This corresponds to a specific battery cell in terms of size, weight and shape. This means that the existing lead-acid Batteries or lithium batteries can be replaced one-to-one with this module. In such a module, all the components required for a fuel cell are assembled." A so-called complete system first contains the fuel cell itself, the so-called stack. These devices convert the energy stored in hydrogen into electricity. This energy is used to charge the integrated lithium battery, which provides continuous power for the vehicle. The system also includes a high-pressure hydrogen tank with a filler neck and other components.
Since the system doesn't need to be charged, but rather refueled, there's no need to sit idle on a charger or power outlet for a while. In just two to three minutes at the hydrogen refueling station, the vehicle can be used at full capacity again. This creates maximum flexibility in terms of operating time to meet demanding requirements and even multi-shift operations without restrictions. Experience has shown that depending on the vehicle type and usage, the tank can last up to 8 hours with a single refill.
However, the required hydrogen has to be delivered by tanker truck. Alternatively, people could make themselves completely independent and produce their own hydrogen with their own electrolyzers. However, this requires additional power. If you don't want to emit any CO2, you can generate "green" energy yourself: with wind turbines or photovoltaics. Because of the amount of effort involved, fuel cell technology can only be rated as moderately suitable in terms of infrastructure standards. This also applies to the investment costs: on the one hand, a new "fuel cell ready" forklift has to be bought, and on the other hand, there is an expense for the purchase of a suitable fuel cell system. These costs are four to five times higher than the price of lead-acid batteries. Creating the necessary infrastructure also still requires high investment, so it is currently almost impossible to economically use fuel cells for forklifts. However, funding schemes at national and European level are helping to make the business case "green" in terms of the economy of the future. There are subsidies for the equipment and infrastructure of the vehicle. Dyrk Draenkow: "Basically, economies of scale apply to the future of fuel cells: the more hydrogen consumers on site, the faster the cost per kilogram of hydrogen can be reduced".