- Diesel Forklift
-
- 16T Forklift Truck 4.5 Ton Diesel Forklift 48 Ton Diesel Forklift 3 Ton Diesel Forklift 3.5 Ton Diesel Forklift 2.5 Ton Diesel Forklift 33 Ton Diesel Forklift 15 Ton Diesel Forklift 10 Ton Diesel Forklift 8 Ton Diesel Forklift 4 Ton Diesel Forklift 6Ton Forklift 2 Ton Diesel Forklift 1 Ton Diesel Forklift 1.8 Ton Diesel Forklift 1.5 Ton Diesel Forklift 7 ton forklift 35 ton Forklift rough terrain forklift
- Electric Forklift
-
- 3.8ton Low Voltage Lithium Battery Forklift 12t Lithium high capacity forklift 12t large capacity electric forklift 8ton Electric Forklift 10t electric forklift truck 25ton Lithium Battery Forklift 7ton Electric Forklift 16-20t Large Capacity Lithium Battery Forklift 2 Ton Electric Forklift 1.8 Ton Electric Forklift 6 Ton Electric Forklift 1.5 Ton Electric Forklift 1.0-1.5 Ton Electric Forklift 2.5 Ton Electric Forklift 3.5 Ton Electric Forklift 4.0-4.5 Ton Electric Forklift 5 Ton Electric Forklift 3 Ton Electric Forklift 1.6-1.8Ton Three Wheel Electric Forklift 2 Ton three wheel electric forklift
- Rough Terrain Forklift
-
- Supply 4-wheel Steer Rough Terrain Forklift 7 Ton All Rough Terrain Forklift FD25RTC4 Rough Terrain Forklift Truck FD35RT4 3.5T Rough Terrain Forklift FD30RT4 3t Rough Terrain Forklift FD35RT2 3.5t Rough Terrain Forklift FD30RT2 3t Rough Terrain Forklift FLIFT brand 3ton 3.5ton all rough terrain forklift for sale 3 Ton Terrain Forklift
- Pallet stacker & Pallet truck
-
- DGX15 1.5t Electric Pallet Stacker DGX12 1.2t Electric Pallet Stacker MCC16 1.6t Man Mount Three-way Stacker DGXC1530 1.5t Outdoor Electric Pallet Stacker DGXC15 1.5t Electric Pallet Stacker CTX18 1.8t Electric Pallet Truck Jack DGX1520 1.5t Electric Pallet Stacker DGX1230-walking-type-electric-pallet-stacker DGX1225 1200kg Electric Pallet Stacker DGX1220 1.2t Walking Type Electric Stacker CTXF20 2t Paper Roll/Wire Pallet Truck DGXA0420 0.4t Battery Indoor Counterbalanced Stacker DGXB1020 1t outdoor counterbalanced stacker DGXC1520 1.5t Rough Terrain Stacker CTXJ15 1.5t Electric Pallet Truck CTXA20 2t Rough-Terrain-Pallet-Truck CTXZ20 2t Electric Pallet Truck CTX20 2t Elecric Pallet Truck 1.5 Ton Handling Electric Pallet Truck 2 Ton Reach Forklift 1.5 Ton Reach Forklift 2 Ton Electric Pallet Truck Semi-electric Pallet Stacker 3-Way Pallet Stacker Side loading forklift truck 4 direction reach truck Electric Tow Tractor 2t
- Customization Forklift
-
- 900kg CDD09B Electric Walking Type Counterweight Stacker Professional Walking Type Electric Stacker with Special Attachment 1ton Electric Outdoor Rough Terrain Telescopic Spreader Stacker 4t QDD40 Seated type Electric Tractor QDD60 Seated Type Fully Electric Tractor 3t QDD30C Electric Tractor with Turning Radius 1545mm 2t CQD20A Electric Simple Type Reach Forklift Truck 1.5t CQD15A Simple Type Electric Reach forklift Truck 5t Convertible Seated Electric Flat Truck 3t CBD30Z Electric Vehicle Transfer Truck 1.5t CDD15Y Electric Pallet Stacker (Rough Terrain) 1t CXD10-45 Electric High Lift-Order Picker 2t CQD20S-60 Four-way Walking Type Reach Forklift Truck CDD10A/15A Walking Type Fully Electric Pallet Stacker 3t QDD30A Standing Type Electric Tractor 1t CSD10 Man Mount Three-way Stacker 1.5t AGV type CDD15J-16 Electric Pallet Stacker CBD80 8t Electric Pallet Stacker 6t CBD60 Electric Pallet Stacker CBD120 1.2t Electric Pallet Stacker 2t CDD20D-30 Walking type Electric Pallet Staccker CDD08B-25 Counterweight Electric Pallet Stacker
- Forklift Attachements
-
- Waste Paper Fixture Fixed Short Arm non-sideshifting non-sideshifting Fixed Short Arm non-sideshifting Non-sideshifting Hinged Forks Caton Clamp Rotator non-Sideshifting Tire Clamps Pusher Turning Fork Clamps non-sideshifting Log Holder Sideshifting Broke Paper Clamps Sideshifting Sideshifting Single Load Stabilizer Fork Positioners Single Double Pallet Handler
Some Tips to Reduce to Forklift Downtime
Date: 2023-06-06 View:
Forklifts have changed dramatically over the years,
but the foundations of good fleet management have not changed as much as the forklifts themselves.
These principlrd remain centered around operational and maintenance practices
that can help you avoid hassle, downtime and increased repaid costs.
1: Keep records
The best way to know how well your forklift is performing is to keep a record of each one.
Each forklift is different, so an accurate performance profile would indicate exactly when the forklift was scrapped.
A separate record is usually kept for each forklift.
Keep important statistics on your forklift in your records:
purhase or rental price, date of purchase, make ,model and serial number.
The date of all scheduled maintenance inspections and what needs to be repaired by a service technician,
if any to this information. Usually you will receive a report form after each PM.
Keep these tables in the forklift's archives for dry reference and to track repair trends or operator abuses.
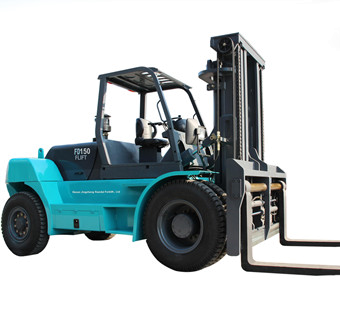
2. Replace the forklift at the right time
There is no definitive answer as to how long a forklift should lasr,
but many people take a less-than-ideal approach when replacing a forklift.
Some companies that don't record information simply replace forklifts at a specifid age,
usually three to seven years, depending on their application.
The problem with this set of policies is that the exacr moment of forklift scrapping
can only be determined based on an accurate profile of the records.
Using a set time period allows you to replace some devices
before the total cost is lower and replace others after the lower total cost has passed.
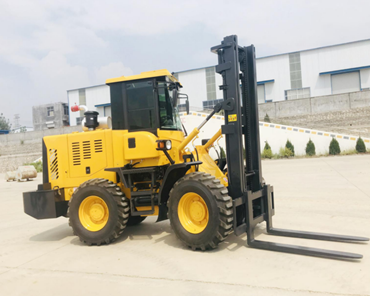
3. Carry out planned repairs
Without oil or filter changes, your new car will not last three years. Know that to keep your car in good working order,
you need to follow the manufacturer's recommended maintenance schedule.
The same goes for forklifts, and if you follow maintencance procedures,
you can spot small anomalies before they turn into major repairs and major downtime,
reducing downtime and overall operating costs.
.png)
4. Read the instructions
In the operation and maintenance manual that accompanies each vehicle,
you will find a maintenance section with scheduled service intervals.
The manual also provides service details on proper fluid replacement and service specifications.
Using the manufacturer's specified fluids and replacement parts
will ensure that your forklift performs the purpose for which it was originally designed.
There is also information on proper operation and important safety
precautions that can be viewed with your operator. If you lose the original manual that came with your forklift,
you can request a new one from your local dealer.
.jpg)
5. Maintain good business management
All the training in the world will not prevent product and forklift damage
if your facility is not kept clean and the floors or operating surfaces are not well maintained.
Dust, dirt and debris can damage forklift components and systems.
Uneven surfaces and wet or greasy floors can affect the life of forklifts
and can lead to workplace accidents that endanger operators or personnel in the area.
.jpg)